Better than ever – AFRISO presents the upgraded pressure transducer DMU 13 Vario
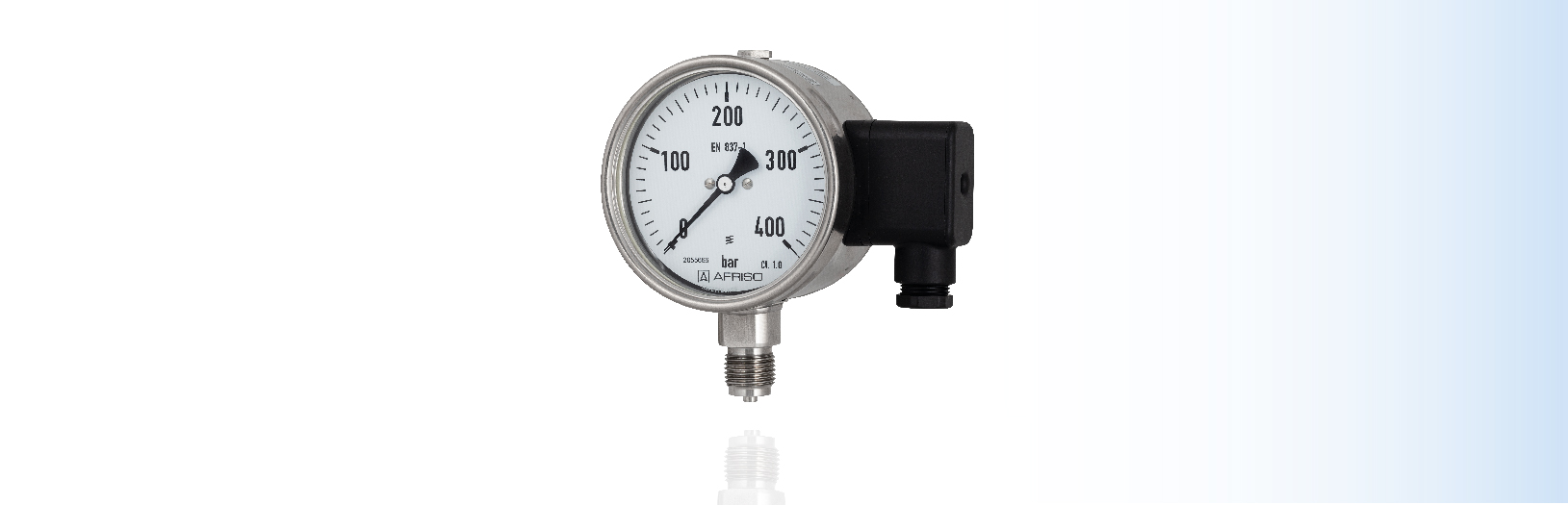
Process efficiency and process reliability in industrial production are decisive competitive factors. Condition monitoring is therefore taking centre stage in more and more areas. Even minimal deviations of individual parameters such as temperature or pressure can adversely affect production results, disrupt production processes, damage machines and systems and pose hazards to persons. As a partner of the industry, AFRISO-EURO-INDEX GmbH from Güglingen has been developing and producing measuring and control devices for pressure, temperature and level for more than 150 years. Continuous further development and optimisation of the products plays just as important a role as the innovative development of new technologies.
"We consistently use technological potential to improve our products," explains Jürgen Fritz, managing director and owner of the company run by a family in the fourth-generation. "This way, we keep succeeding in making our measuring and control technology even more reliable and accurate, and in consistently increasing its functionality and applicability in the interests of our customers."
A typical example of the practical implementation of this company philosophy is the revised pressure transducer DMU 13 Vario, an upgrade of its predecessor DMU 13, which AFRISO is currently presenting and including in the comprehensive product range.
Pressure transmitters are used in a wide range of industrial applications to monitor relative pressure or absolute pressure or differential pressure, both in the range of just a few millibars of pressure difference and in the case of extreme pressure.
"Our model DMU 13 has proven itself in a wide variety of application scenarios over the past years," reports Christian Blasinger, Head of the Division Industrial Technology. "For example, in process pressure monitoring of pigment suspension to ensure the quality of the end product or in the combination of two DMU 13 to monitor the saturation of a bag filter, both at a leading manufacturer of printing inks." As a combination of a mechanical, current-independent local display based on a Bourdon tube safety pressure gauge and an electrical output signal, the pressure transducer offers maximum readability and optimum options for implementation in existing digital systems.
With the presentation of the revised version DMU 13 Vario, AFRISO is, above all, clearly expanding the measuring range of the pressure transducer. While the measuring range of DMU 13 was up to 40 bar, DMU 13 Vario allows for measurements of up to 400 bar. The measuring accuracy of the pressure gauge remains unchanged, and the measuring accuracy of the transducer improves to less than ± 0.3% FSO according to IEC 60770. AFRISO was also able to significantly improve the accuracy in the temperature error band from ≤ 1 % FSO/10K to ≤ 0.15 % FSO/10K by revising the pressure transducer.
The improved performance of the DMU 13 Vario can essentially be attributed to the use of a piezo-resistive polysilicon thin-film measuring cell, which replaces the piezoresistive stainless steel measuring cell of the DMU 13. The new measuring cell is also the reason that pressure transmission liquid is not necessary.
"With the DMU 13 Vario model, we would like to open up new application possibilities with proven technology in the interest of our customers. A magnet is now used for rapid zero calibration – this saves time, for example, during startup of systems," emphasizes Christian Blasinger.
To the product